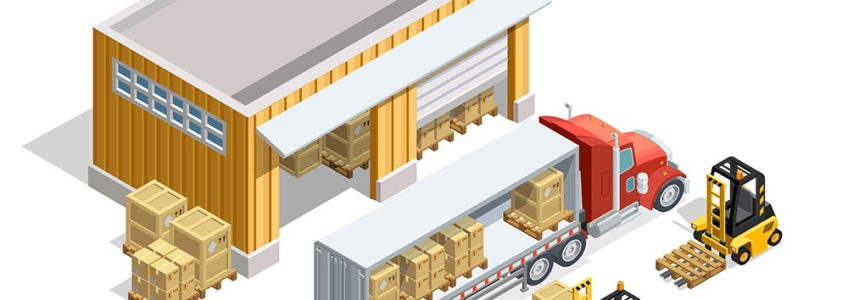
Americans are completely unaccustomed to not being able to get what they want, when they want. In fact, they often get a bit indignant when they must go to more than one store to get a child’s highly desired gift at Christmas and social media is full of complaints about delivery mistakes and delays from Amazon and UPS. Supply chain interruption was, in some cases, far more unnerving during the pandemic than the shutdown itself.
Now that we are in a post-pandemic environment, Americans are struggling with the results of extended supply chain issues as well as willful labor shortages which has changed the face of commerce forever. It is only now that we have come to realize how essential it is to have the ability to crisis manage and the ability to pivot to a contingency plan. Managing a supplier shutdown can be a challenging situation, but there are steps that you can take to minimize the impact on your business.
-
- Keep an active/current list of all suppliers. Review contracts with each and request copies of their service interruption crisis plans. Determine if there are any legal clauses in your respective contracts covering this situation. Does the contract include language allowing you the option to locate a different vendor during a supply chain interruption? If not, amend the contract to include a supply chain interruption clause.
- Assess the impact on your business. Analyze the impact of the supplier shutdown on your business. Determine which products or services will be affected and how much it will cost your business.
- Prioritize critical operations. Prioritize critical operations and products that are essential for your business. Allocate resources and focus on activities to ensure that these critical operations are not impacted by the crisis.
- Evaluate risks. Calculate the risks associated with your supply chain and take steps to mitigate them. Identify potential risks, such as natural disasters, geopolitical events, or economic downturns, and develop strategies to minimize their impact on your supply chain. Key areas that a comprehensive risk assessment should consider are the following:
-
- The severity of the shut down: and the anticipated time limit, the impact on inventory levels. Assess how much inventory you have on hand and will it meet customer demand based on projected time limits for the interruption.Measure the fiscal impact: How much revenue will you lose and what will it cost you to find and implement production with a new vendor?
- Customer impact. Calculate whether you will be able to meet customer demands and how much customer loyalty may be jeopardized.
- Supplier relationship impact. Determine whether suppliers are likely to resume normal operations and how much it will cost to find new ones if necessary.
- Legal and regulatory impact. Identify if the shutdown will impact your compliance with legal and regulatory requirements. Determine whether you need new licenses or permits to continue operations.
- Reputational impact. Evaluate if customers and stakeholders view the shutdown as a negative reflection on your business.
-
- Identify alternative suppliers. Start by identifying other suppliers who can provide the same goods and/or services as the supplier that has/may shut down. Look for suppliers who have a good reputation and can provide the same quality of products or services.
- Negotiate with your suppliers. If you are unable to find an alternative supplier, consider negotiating with your existing suppliers. Ask them to increase their production or offer you better pricing to help manage the impact of the supplier shutdown.
- Develop a communication plan for your stakeholders. Connecting with your stakeholders, including suppliers, customers, and employees, about the crisis and what steps you are taking to address it is crucial. Be transparent with your customers about supplier shutdowns and the steps you are taking to mitigate their impact. Provide them with a timeline, even if fluid, of when to expect to resume normal operations.
- Create a solid contingency plan. Develop a contingency plan to minimize the impact of any future supplier shutdowns. This plan should include identifying alternative suppliers and developing relationships with them, as well as having a plan for communicating with customers and managing costs. A reliable effective contingency plan outlines the steps you will take in case of similar crisis in the future. This plan should include strategies for identifying alternative suppliers, managing inventory, and communicating with stakeholders.
- Stay informed. Keep up to date with any news or developments related to the supplier shutdown. This will help you to make informed decisions and minimize the impact on your business.
- Situation monitoring. Monitor the situation and evaluate the effectiveness of your response. Continuously assess the impact of the crisis on your supply chain and adjust your response as needed.